






|
The following software software applications have been developed in house by CTS:
Waterflood and PWRI Induced Fractures
Water injection wells often operate above fracturing pressure.
In deep high permeability reservoirs this is caused by injection
temperatures significantly cooler than the hot formation resulting
in thermo-elastic stress reduction around the wellbore. In low permeability
reservoirs it is caused by build up of high pressure transients
that exceed the poro-elastically changing in-situ stress.
CTS has developed a state of the art screening model TRIFRAC that
simulates this process and can additionally predict (a) the effect
of fines impairment due to injection of dirty water (Produced Water Re-Injection: PWRI) and (b)
the eventual loss of vertical fracture containment as the fracture
grows to a critical length. The fines impairment model accounts for
both internal and external filtercake.
TRIFRAC couples water injection into the formation with volume
storage in the fracture so that hydraulic fracturing
of bounding shale intervals can also be considered.
The original FORTRAN model has now been converted to C#.NET and
incorportated into a Window environment that enables common data to
be used between a suite of geomechanics applications. Data input and
graphical output are enabled via interaction with a formatted Excel
file with easy units conversion capability.
|
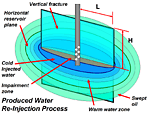
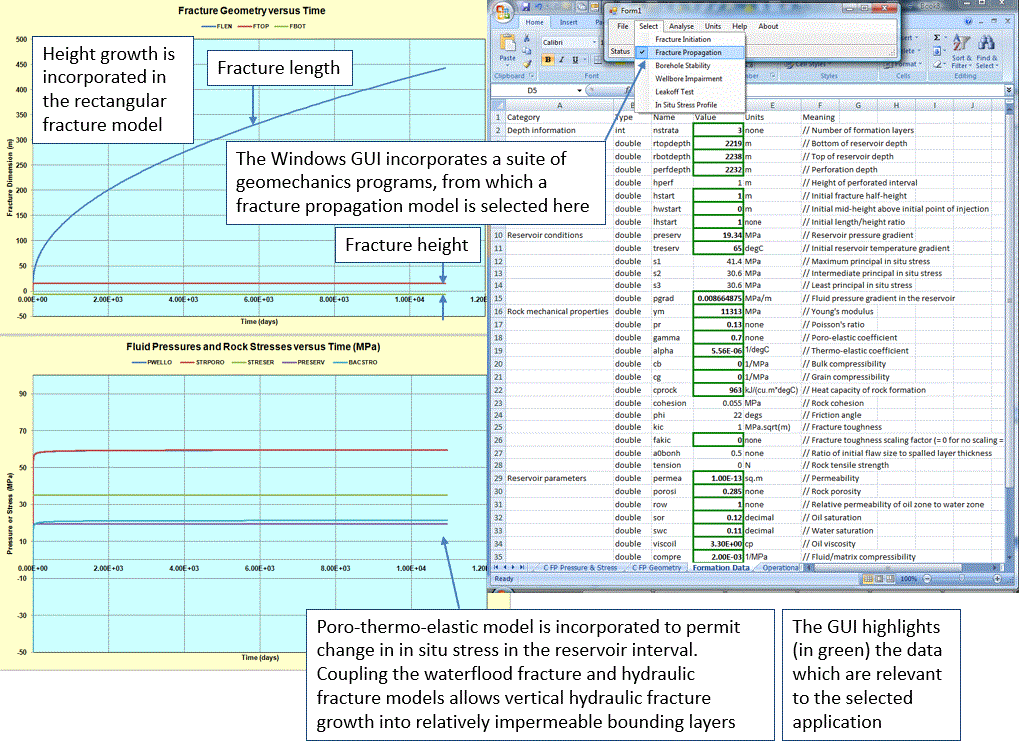
TRIFRAC
|
Reliable and accurate prediction of hydraulic fracture growth
and containment are crucially important for successful development of
oil and gas reservoirs, both conventional and unconventional, for
waterflood and PWRI induced fracturing operations, for drill cuttings
re-injection projects, in hot dry rock geothermal projects and for
future carbon capture and storage in saline and also basalt rock
formations.
CTS has developed two planar 3D hydraulic fracture simulators,
GEOFRAC and AQUAFRAC, with the objective to achieve robust and
efficient solutions to the hydraulic fracturing problem. GEOFRAC
is based on an expanding finite element mesh that contour fits
the fracture boundary, whereas AquaFrac is based on a fixed
rectangular grid of elements that replicate the fracture shape
by opening up inside the fracture boundary.
GEOFRAC has been uniquely designed to solve for the fracture boundary
movements implicitly within the coupled solution procedure on each time
and a publication (SPE 24989) in 1992 showed how accurate satisfaction
of the coupled elastic, fluid flow, volume balance and fracture propagation
constraints could be obtained with GEOFRAC compared to another commercial
model that was commonly in use at that time.
Whereas GEOFRAC was designed for optimal vectorised performance on a
supercomputer, AQUAFRAC has been designed from the outset to acheive optimal
efficiency in a PC environment.
Both simulators provide similar results and have been constructed
with a modular coupled architecture that could permit them to be
further enhanced and developed to simulate a wider range of
functionality. In particular, AQUAFRAC’s rectangular grid structure is
expected to offer optimal performance if combined with reservoir
simulator grids, for example in future to solve the notoriously challenging
fully coupled 3D numerical waterflood fracture problem.
|
GEOFRAC
AQUAFRAC
|
CTS is advancing state of the art of borehole stability modeling
by introducing new types of constitutive laws that offer far more
accurate descriptions of rock failure than can be achieved with
traditional elasto-plastic models.
For sand formations, CTS plans to test a combined clay and sand
critical limit state model (CASM) developed by Nottingham University.
A significant example of this constitutive model compared to its predecessors
is its ability to describe the full range of constitutive behaviour from loose
sand throught to stiff clay with just five physically meaningful parameters
that can be determined from laboratory experiments.
As part of this effort to test these constitutive models, a 2D planar
finite element model, STABROC, has been developed, which is also capable
of providing ultra-fine mesh simulation of near-wellbore hydraulically
induced fractures.
For more brittle rocks, a semi-analytical model MUDWELL has also been developed
that calculates the optimal mudweight for a borehole of any inclination and azimuth
associated with a fracture spalling mode of failure, based on an original
theory for a vertical borehole by Dyskin, Germanovich and Roegiers.
Also for more brittle rocks, an internal variable constitutive damage model
is being developed with the objective to incorporate nonlocal behaviour relating
to the heterogeneous scale-dependent and possibly fractal nature of progressive
multiple fracture growth and interaction.
It is also intended that such a model should appropriately simulate observed
degradation of elastic rock stiffness with increasing crack density, in addition
to more conventionally assumed elasto-plastic behaviour.
|
CASM
STABROC
MUDWELL
|
CTS has developed a capability to predict formation breakdown
pressure in deviated wells of any inclination and azimuth, depending
on the magitude and orientation of the principal rock in situ stress
directions.
INIFRAC enables these calculations to be performed both for the case
of an impermeable mebrane (i.e. a filter cake) forming during drilling
and completion operations on the wellbore wall, and for the case where
wellbore fluids are freely able to enter and also be produced back from
the rock formation, as in clean-up operations.
In the former case, the total stresses acting in the formation at the
wall are used to compute the formation breakdown pressure. In the latter
case, account is also taken of the poro-thermo-elastic stress changes in
the rock. Generally speaking, lower formation breakdown pressures are
computed when fluid is able to penetrate the formation.
INIFRAC also includes several other useful features, such as a model for
predicting fines impairment during PWRI operations and the consequent reduction
in near wellbore permability and increase in injection pressure (thereby allowing
the time before formation breakdown to be computed). It is also possible to use
INIFRAC to back calculate the state of in situ far field intermediate stress using
data from Extended Leakoff Tests (XLOTs).
The original FORTRAN model has now been converted to C#.NET and
incorportated into a Windows environment that enables common data to
be used between a suite of geomechanics applications. Data input and
graphical output are enabled via interaction with a formatted Excel
file with easy units conversion capability.
|
INIFRAC
|
DEEPSTRESS determines the in situ stress profiles for all three
principal stresses based on calibration of sonic log data with available
XLOT data.
Often, sonic log data is collected with different depth intervals from
other data such as density logs, for example data collected while drilling
may have different depth references from log data collected using a wireline.
DEEPSTRESS has been designed to resolve these depth differences by interpolating
all such data to the same depths as the sonic log data. This is not a task
that can be easily performed using a spreadsheet and if not conducted carefully
within a well tested computer program, this simple issue can produce erroneous
results that may not be easily detected or understood.
Having resolved the data as described above, DEEPSTRESS then computes the
vertical overburden stress Sv from the density log data. Using the horizontal
stress (Shmin and SHmax) data obtained from inversion of XLOT data using INIFRAC,
as explained above, DEEPSTRESS then solves for the corresponding horizontal tectonic
strains from the classical elastic formulae. The routine then uses these tectonic
strains to resolve the profiles of Shmin and SHmax over the depth of all intervals
for which both sonic and density log data are available.
|
DEEPSTRESS
|
MPDAnalyser is a C#.NET application interfacing to Excel via the
Microsoft Object Model.
It enables rapid interpretation of drilling pressure and flowrate data with
the objective of identifying instances of gradual and sudden fluid and solid
influx ("kick"), hole collapse, wellbore expansion (“ballooning”), fluid losses
to the formation, fracture initiation, fracture closure and presence of multiple
fractures.
MPDAnalyser is a prototype model that might provide a first step towards a
fully automated, real-time wellbore diagnostic system, perhaps linked to a machine
learning algorithm capable of synthesising large data sets collected from numerous wells.
|
MPDAnalyser
|
A Petrov-Galerkin finite element model, CRUCIBLE, has been developed by
CTS to simulate thermal convection processes associated with circulating supercritical
water in fractured rock interfacing to a zone of molten material. It's primary purpose
is to investigate the feasibility of achieving stable production of high enthalpy steam
above 500 degrees C from ultra-deep seated geothermal wells penetrating the carapace of
a magma caldera.
This process was first promoted and extensively researched by Sandia National
Laboratories in the 1970s and 80s as part of the US Star Wars programme, with
the objective of achieving US energy independence with low CO2 producing
non-hydrocarbon sources. Although the Sandia project ended in 1992 as a result
changing US political priorities, it has now been proved to work by the Iceland
Drilling Project.
The process has genuine potential to contribute significantly towards mitigation of
climate change through reduction of CO2 emissions on a global scale and could help many
developing countries in regions of active volcanic activity to achieve energy independence
and grow a clean energy economy.
Much research remains to be done in this area to establish the technology on a truly
sustainable pathway. A significant feature of CRUCIBLE is that it includes a thermal
mixing term that emulates thermal diffusivity through a fracture network.
Further research effort could focus on calibrating this attribute of the model with
laboratory scale experiments and micromechanical models of fracture networks. It could
also be related to the work described above to create a constitutive model for thermally
induced progressive fracturing of rock.
The solidification process at the molten rock
interface is presently based on a classical latent heat model, but may also need further
investigation in the context of a real downhole environment, as may also the
possibility of chemical reaction between the injection water and the molten material
under high downhole pressure conditions.
|
CRUCIBLE
|
Effects of scale are well known in oil and gas reservoir simulation.
Rock permeability measured at core scale often differs from permeability
interpreted from well tests, which in turn can vary significantly from
reservoir scale permeability estimated from matching reservoir simulation
results against production history data.
Conventionally, this is handled by various upscaling techniques, all of
which ammount to a form of aggregation of permeability data at once scale
in order to provide an estimate of the permeability at a larger scale.
An alternative approach is to consider possible forms of Darcy’s law
that depend on a fractional as opposed to the conventional first order integer
derivative of pressure. A possible advantage of this approach could be inherent
applicability over a heierarchy of scales, thereby offering a potential solution
to the upscaling problem. A disadvantage is its implicit nonlocal (fractal)
characteristic that can lead to considerably larger computer overhead than
a conventional integer derivative reservoir simulation approach.
CTS has developed an experimental radial miscible gas solution based on assuming
fractional derivatives in pressure for defining Darcy flow for each of the three
phases (oil, water, gas). A computer code, EREBUS, has been constructed and is
undergoing testing using this technique. An extension of the model to three
dimensions is also in progress.
|
EREBUS
|
REVELATION is a Bayesian decision network model under development by CTS
aimed at capturing the complex interaction between decisions and the events
that lead to actions that in turn lead to further events. The intention is
to enable a rigorous mathematical structure within which to define and calibrate
such interactions on the basis of real-world experience and data, so as to
to optimise decision-making over a wide range of time-scales with respect to a
stated mission objective.
A typical problem might be to deterine the present Risk R of Consequences C
occurring, given the present Status S and if Actions A are undertaken in a manner
which is consistent with achieving Objectives O within Limitations L. This differs
from a conventional engineering design approach to risk assessment in that the Status
of a system and Actions that can change the condition of a system are not assumed to
remain static over the life of the facility. It also allows introduction of short
and long range interactions between events and actions, as well as a measure of the
degree of such interactions.
Procedures for fitting such a model to real time data may also draw on advances in Bayesian
forms of neural networks. Whereas these methods often aim to find categories and trends
in data using Gaussian statistical assumptions whilst ignoring outliers, a different
approach may need to be considered if aiming to focus on predicting and managing extreme
events. In this context, possible links with chaos modelling are also being investigated.
An important application could be to enable real-time assessment of human response and
consequent guidance in emergency situations, also to provide AI assistance in the avoidance
of such situations.
|
REVELATION
|
CTS has built up considerable experience in assessing the
potential hazards that may be encountered when drilling through
near seabed natural gas hydrate formations and subsequent problems
that may also ensue in these formations during long term production
of hot reservoir fluids from deeper zones.
During drilling operations, hot drilling fluids returning via the
open annulus of a top hole section can cause near seabed hydrates to
dissociate, allowing gas and also residual water to ablate towards the
wellbore, potentially causing washouts.
During production operations, hot reservoir fluids flowing to surface
can cause near seabed hydrates to dissociate on the outside of the casing,
causing loss of cement bond and integrity of the wellhead. As the
dissociated gas and water cannot flow into the annulus in this scenario,
pressure can also build up behind the surface casing, potentially leading
to more serious loss of structural integrity of the well completion.
In either case, a worst case scenario could involve a serious loss of well
control, either due to loss of containment of the drilling or reservoir fluids,
or to significant emission of natural gas from the hydrate itself and any
shallow free gas deposits to which it may be connected.
To assist in assessing the seriousness of this geohazard, CTS has
developed an analytical model HYDISS that simulates the progress
of a hydrate dissociation front away from a wellbore in response
to wellbore fluid temperatures exceeding the hydrate dissociation
pressure temperature relation.
Complementary to this capability, another analytical model GASPLUME has
also been developed by CTS to estimate the concentration of gas that is likely to
affect buoyancy conditions at sea level due to gas emissions of this nature occurring at the
seabed. Partly using models such as these, CTS can provide an overall risk
based strategy for assessing and dealing with near seabed natural gas hydrates
geohazards.
A possible future model, HYSOLVE, could investigate ways of producing methane gas hydrates
by injecting a solvent to stimulate progression of the dissociation front. It could also
incorporate aspects of the CASM critical limit state model for sand and clay proposed for
the STABROC borehole stability model described above.
|
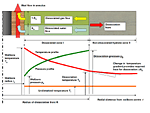
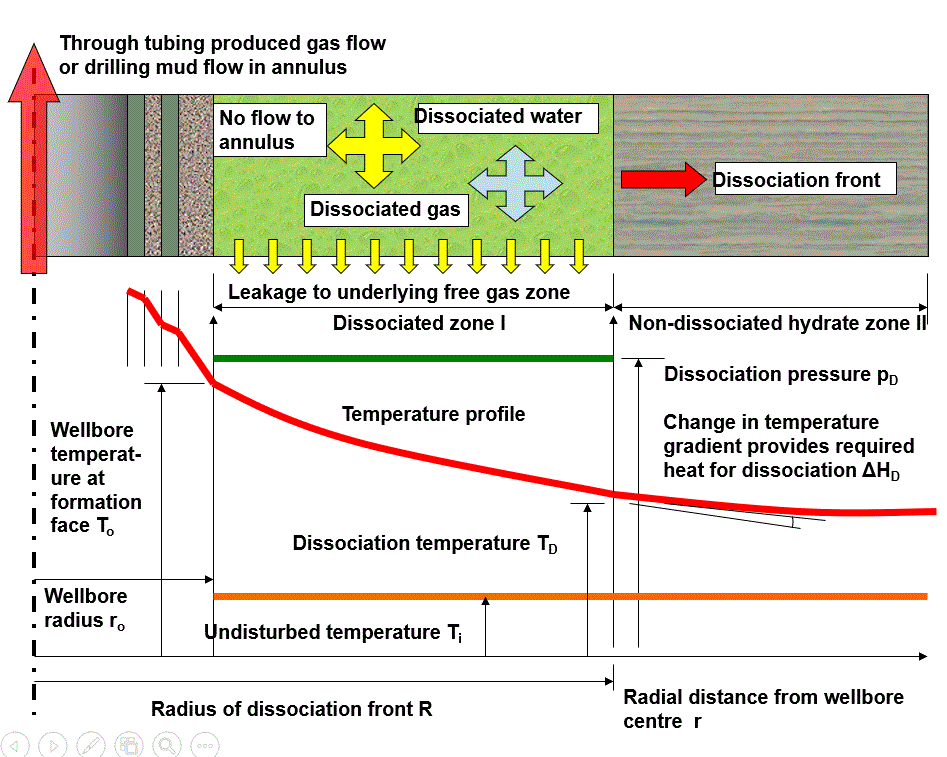
HYDISS
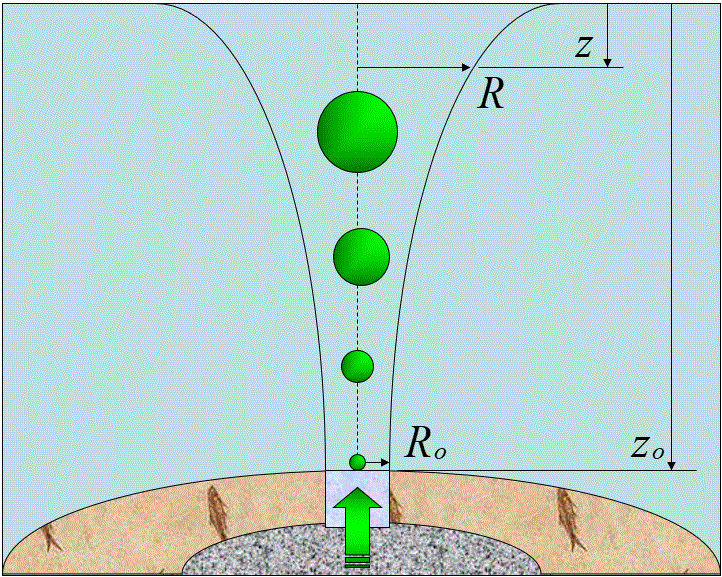
GASPLUME
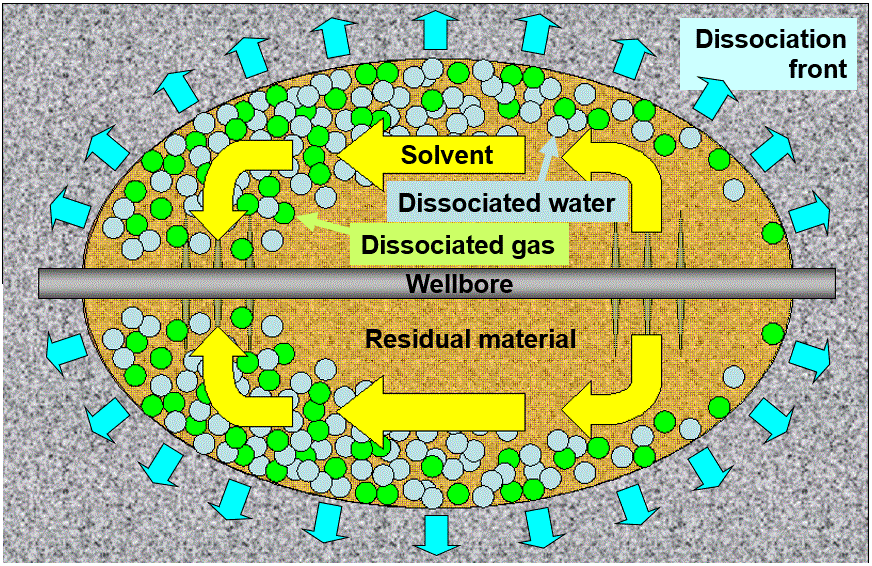
HYSOLVE
|
High Mach number supersonic gas flow in pipes can occur in as a
result of sudden release of highly compressed gas through a valve or choke.
Examples in the oil and gas industry are overbalanced perforating and
fireflooding operations.
CTS has designed a numerical model, GASPIPE, in order to simulate these kinds
of operation. The model is based on consideration of mass and energy balance,
together with conservation of momentum, leading to a set of nonlinear time dependent
differential equations in pressure, velocity and Mach number, with temperature
changes defined in terms of the velocity and Mach number in accordance with the
thermodynamic definition of the speed of sound.
Solutions are obtained using either a finite difference or a finite element
discretisation of the differential equations, with boundary conditions defining
the sudden gas release appropriately defined. Account is also made for changing
cross sectioal area along the length of the conduit, thereby allowing simulation
of a valve or a choke, also for adapting the model to describe gas driven propagation
of a hydraulic fracture, such as may result from overbalanced perforating operations.
Presently the model is configured for ideal gas conditions, but could be readily adapted
to real gas conditions in future versions. Chemical reactions are also not presently
included, but could likewise be considered in future versions. Other applications besides
oil and gas related may also be possible, for example space vehicle propulsion by sudden
realease of highly compressed gas.
|
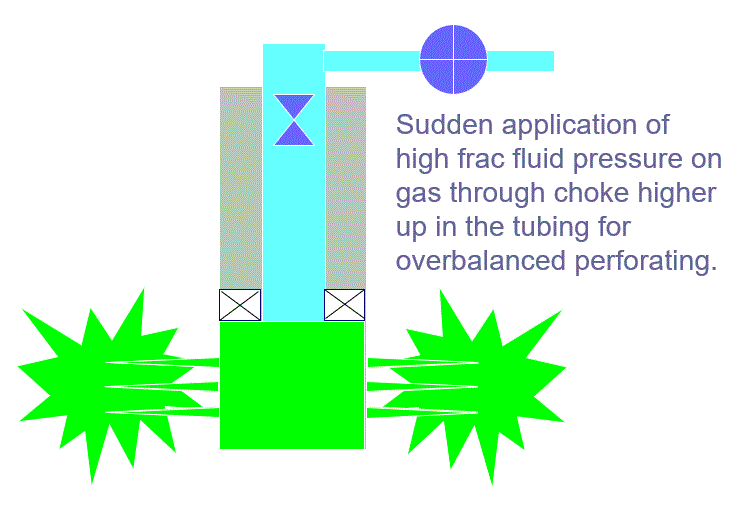
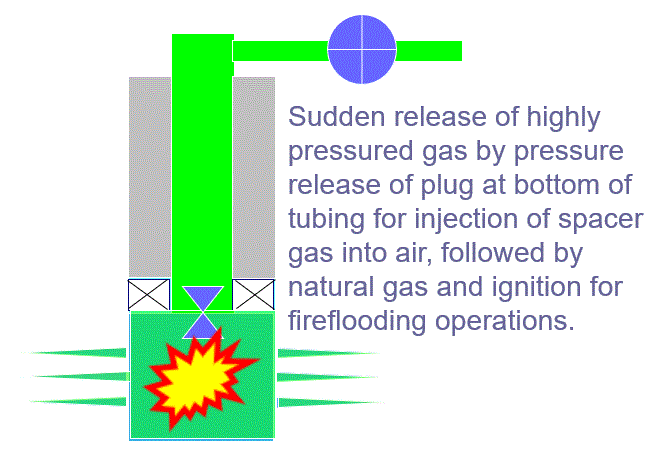
GASPIPE
|
DRILLFLUX is a C#.NET program under development by CTS
aimed at providing standard calculation of well control procedures,
such as Driller's and Wait and Weight methods, for example for the
purpose of creating kill graphs and kick tolerance plots.
It calculates the annulus shoe pressure and equivalent density for a dynamic kick,
following the procedures described in sections 4.6 and 11.3.2 of:
Watson, D., Brittenham, T., Moore, P.L., "Advanced Well Control", SPE Textbook Series,
2003, ISBN 1-55563-101-0.
The solution includes a complete PVT analysis based on either the Dranchuk and Abou Kassem
method, or the Hall and Yarborough method, both of which are commonly used in petroleum engineering.
The present version of the DRILLFLUX considers a vertical well only, but a future version
could be based on a modified form of the solution appropriate for deviated wells. Solutions
have also been developed by CTS for volumatric stripping and bullheading calculations that could
be included in future versions as well.
|
DRILLFLUX
|
CTS has considerable worldwide experience in the design and
feasibility assessment of challenging extended reach wells. All
aspects are thoroughly investigated using state of the art software
including wellpath design using geological visualization tools,
extensive data gathering from offset well data and casing design
using casing stress analysis tools.
Operational requirements are also assessed and defined including
torque and drag analysis for both drilling and running casing, required
rig hoist capacity, wellbore hydraulics, pump sizing, liner specifications,
hole cleaning and borehole stability. Additionally, CTS has developed in
house the basis for a hard drillstring model HARDRILL for which potential
applications are being sought.
Potential interest in supporting a project to develop a model to automate
the optimisation of well locations is also being sought, for which an initial
concept outline has been drafted.
|
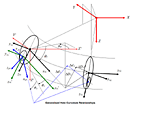
HARDRILL
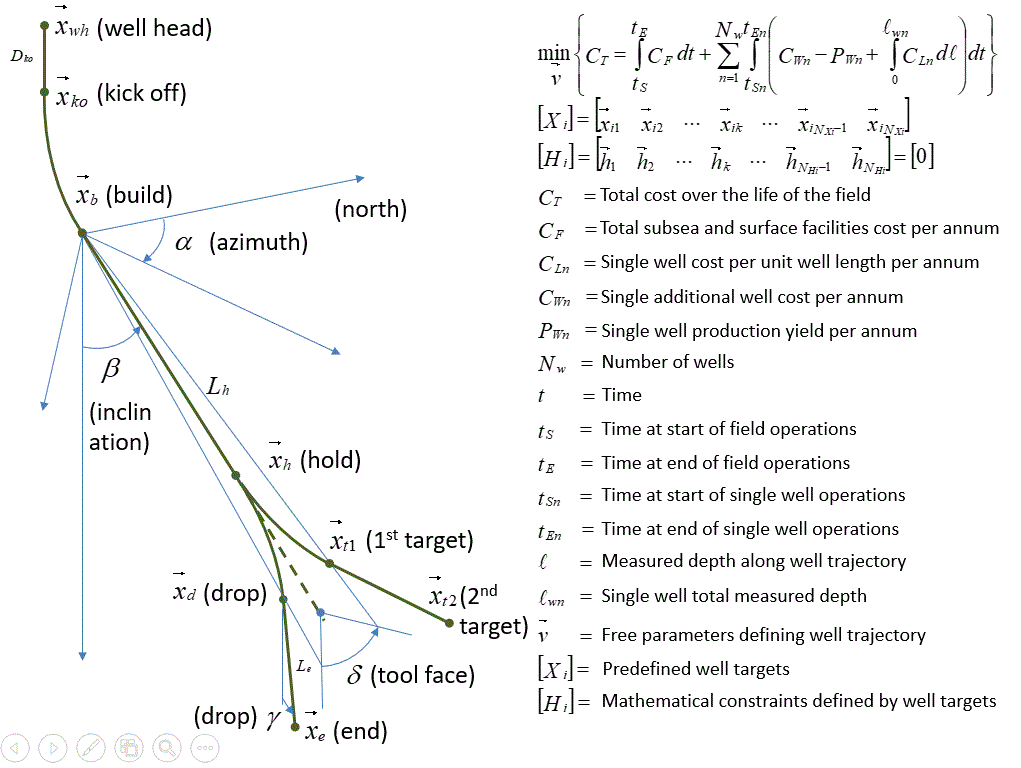
Well Cost Optimiser
|
Production tubing in oil and gas wells can buckle, especially
at the lower landing point in a well completion, due to thermal
expansion resulting from flow of hot reservoir fluids during prodcution
operations.
To provide an assessment of this risk, TUBUCKLE has been developed by CTS
to predict the buckling load at the base of a wellbore tubular having variable
cross section and lying at any inclination to the vertical.
The classic analytical solution to this problem for a horizontal hole predicts
a constant amplitude sinusoidally buckled shape, however numerical solutions such
as the one shown here are capable of predicting a sinusoidal shape with varying
amplitude due to the influence of hole inclination.
TUBUCKLE has been written entirely in C#.NET and iterfaces via a Windows GUI that
controls the manipulation of data input and output via Excel spreadsheets. CTS has
the proven capability to extend this model also to handle curvilinear hole
trajectories.
|
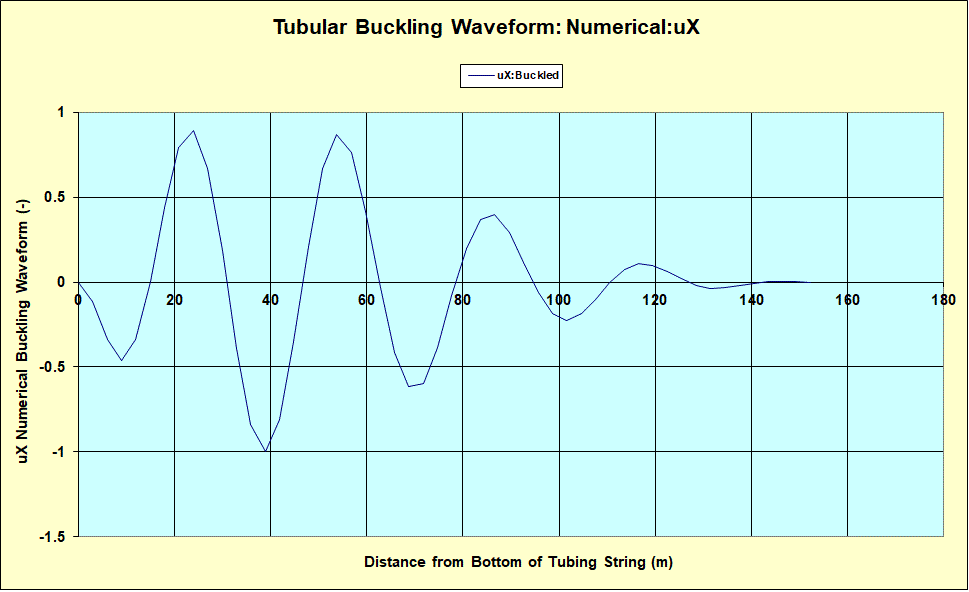
TUBUCKLE
|
CTS has longstanding expertise in the implosion of deepwater structures,
dating back to the Steel~Concrete Composite Sandwich Shell Project at Manchester
University led by the late Professor Peter Montague in the early 1980s.
Originally perceived as a viable technology for development of manned seabed oil and
gas production systems in water depths exceeding 1,000m, the need for this technology
was soon superceded by the development of wet Xmas tree (subsea wellhead) designs that
required no direct human operation at the seabed.
As the oil and gas industry progresses towards projects in ever deeper waters,
possibly as deep as 4,000m and beyond, attention could well turn once again to the potential
benefits of this technology, but now for new applications such as susbsea LNG storage,
ultra-deepwater pipelines and possibly even subsea tankers.
Applications in other areas of
re-emerging interest could include high external pressure and impact resistant structures
for certain types of planetary exploration activities. Other types of new high strength materials,
both for the inner and outer skins and for the filler can also be considered, as can the possibility
of multi-layered sandwich construction to provide potentially indefinitely high collapse resistance.
COMSHL is a finite element program that predicts the structural performance of steel~concrete
composite sandwich cylinders and dome ended shells, based on finite element modelling of the
elasto-plastic behaviour of the inner and outer steel skins and of the interficial concrete filler.
It has been clearly demonstrated using COMSHELL, and with the extensive range of laboratory scale model tests
conducted by Manchester University, that steel~concrete composite sandwich shell structures can withstand
significantly higher implosion pressures typical of deepwater oil and gas developments than equivalent weight ring
stiffened shells.
Part of the expertise within CTS that is relevant to these types of developments relates to deep
understanding of the constitutive behaviour of complex materials such as concrete and other types of
non-linear composite filler materials under long duration conditions of multi-axial stress.
|
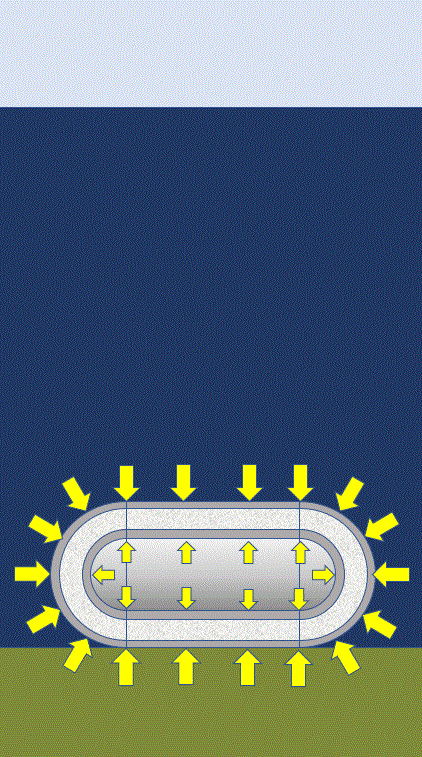
COMSHL
|
|
|